- Individual, highly specialised packaging for brand names
- Automation for fast job changeovers
- 20 per cent less waste
- Flexible production for short and medium run
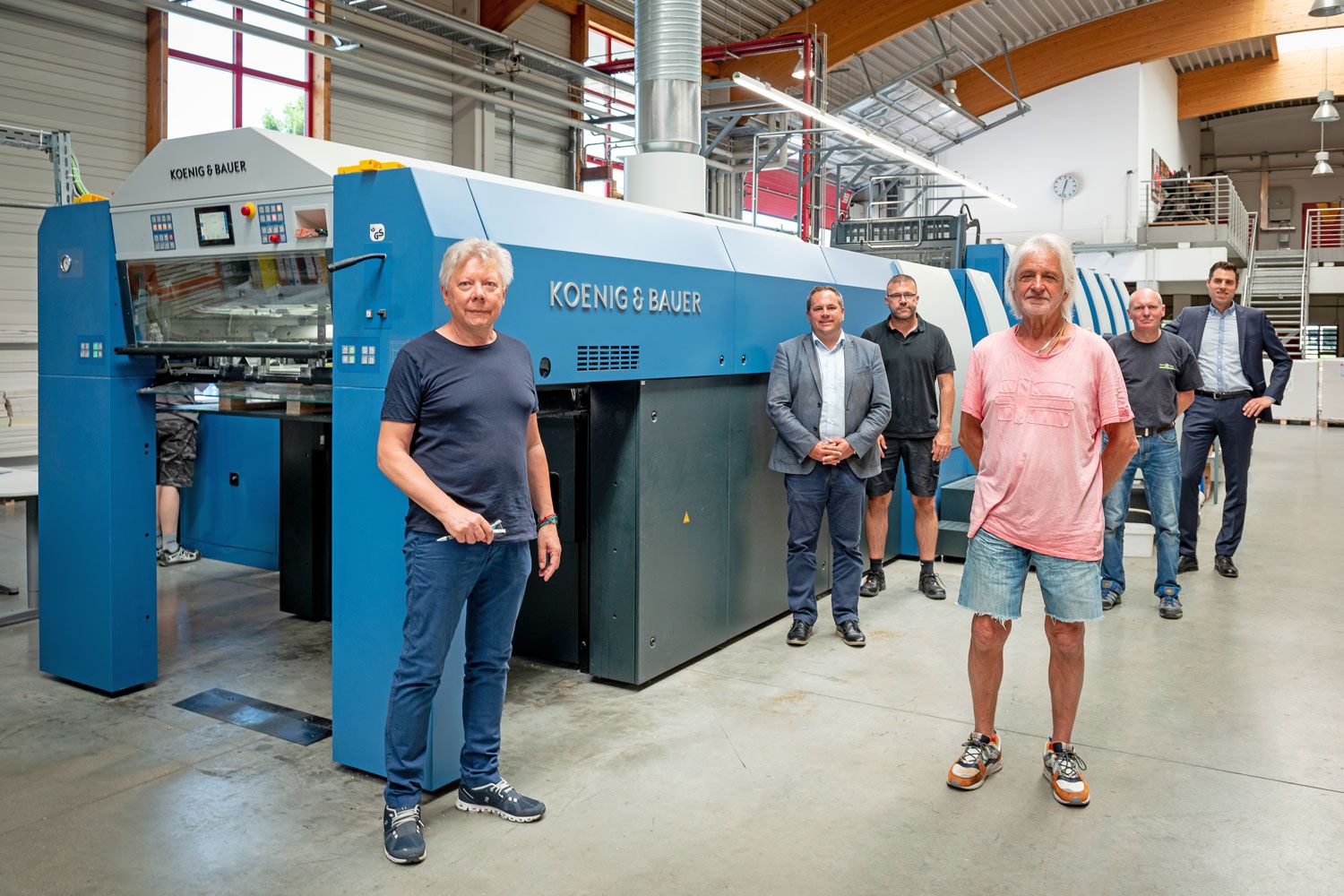
A six-colour Rapida 106 with coating facilities has been used in production at Wittmann Druck & Verpackung since the beginning of the year. The key players in the project recently met up at the press (left to right): managing director Hans Schuster; Gavin Elflein and Ralf Koch, both from Koenig & Bauer Germany; company owner Oskar Wittmann; printer Reiner Schneider; Christofer Hugel, Koenig & Bauer Germany.
Modern, clean and flooded with natural daylight – these qualities characterise the entire company premises of Wittmann Druck & Verpackung in Neumarkt/Oberpfalz. And blue, fast and efficient are attributes that describe the recently installed Rapida 106, which now shoulders all print production for the company. With its inline quality control capabilities, it guarantees both the company and its customers high, reliable and consistent print quality – and ensures this can be done to everyone's satisfaction, because the six-colour coater press now forms the kingpin of a company dedicated to mainly short-run folding carton production. A run of 10,000 copies is already at the top of the range, as managing director Hans Schuster reports. And the print jobs themselves are anything other than routine ones. The company produces very individual and highly specialised packaging for brand owners in sectors such as electronics, writing instruments, confectionery and cosmetics. Advent calendars in a never-ending variety of shapes and forms are one of Wittmann’s specialities.
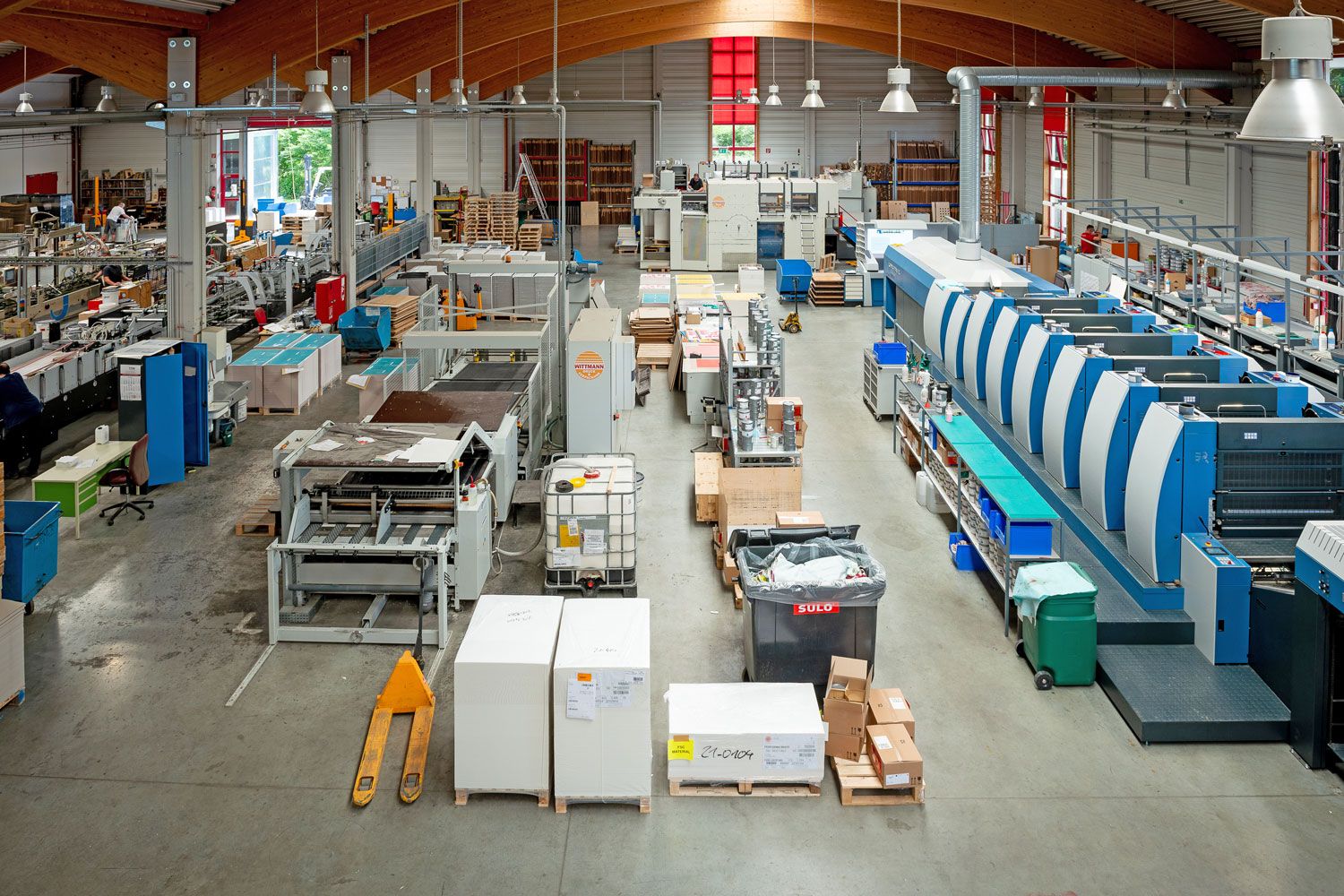
High production speeds and fast job changeovers
The Rapida 106 has brought a number of valuable improvements, especially where short runs are concerned. This is illustrated by the fast and precise colour control, as well as a drastic reduction in the amount of time lost to ink changes at the same time. Key features in this respect are the EasyClean ink duct coatings, which enable exceptionally fast cleaning, and the simplicity of engaging and disengaging individual inking units, which means that production can continue without interruption while the ink is being changed in an unused printing unit.
The sidelay-free infeed DriveTronic SIS and the fully automatic FAPC plate changers are further benefits spotlighted by Hans Schuster and his printshop manager Stefan Zahn, especially when it comes to packaging production: “The press runs much faster than its predecessor. But even more important for us is that job changeover times have been reduced significantly,” says managing director Schuster. The waste savings associated with the new technology – currently around 20 per cent – align perfectly with the company’s eco-friendly philosophy.
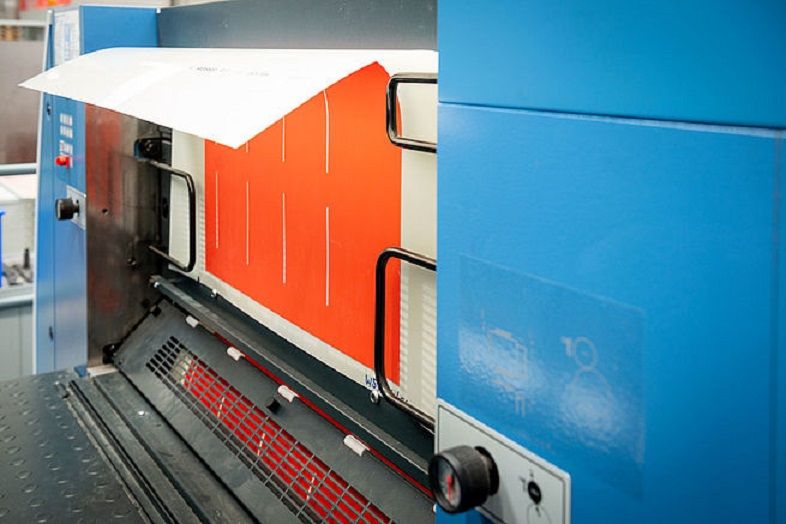
Scoring with flexibility
With 32 employees and a production area measuring 4,200 m2, Wittmann Druck & Verpackung is actually quite a small packaging company. However, it is nonetheless a force to be reckoned with. Almost ten years ago, it was one of the first companies to use migration-safe inks. The sun has been one of the company’s main energy suppliers since 2015 – thanks to a 285 kW photovoltaic array. Heat recovery – also from the new Rapida 106 – allows more energy savings to be made. And baling presses provide the basis for the return of paper and board waste to the materials cycle.
Wittmann also scores points with the high level of flexibility made possible by its extremely lean organisation. The response times – from creation of a job, to data collection and through to production and shipping to the customer – are remarkably short. This is in no small way due to an in-house software solution. New and modified designs for complex packaging forms are developed in the company’s own packaging design office.
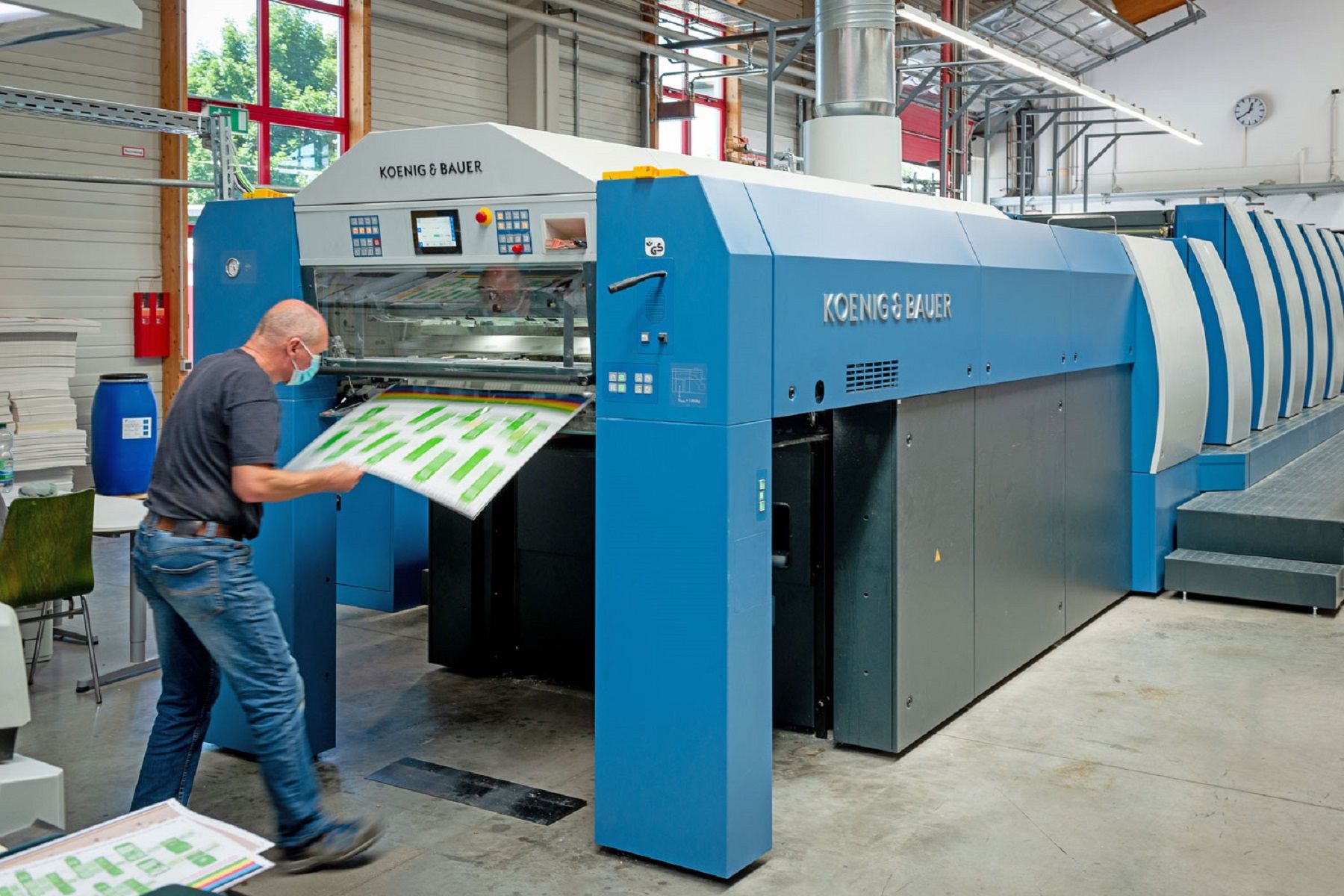
Rapida 106 to mark the company’s 125th anniversary
The full-service production also includes product sorting and filling of the packaging. A mobile shelving system permits up to 1,200 pallets with finished products to be held in intermediate storage. The customers can then have their products delivered at precisely the time when they are needed.
The company was founded 125 years ago, and Oskar Wittmann represents the 3rd generation at the helm. With the Rapida 106, the company has treated itself to a gift worthy of marking the anniversary. The new press, continued regular investments, and the emerging trend to packaging made from renewable raw materials place Wittmann Druck & Verpackung in an ideal position to master future challenges.
Following completion of its investment in the Rapida 106, the management at Wittmann Druck & Verpackung can now move on to make other major investments in post-press equipment. For the moment, however, owner Oskar Wittmann is planning the erection of a second production hall in 2022. As he recently announced to the workforce: “I am now, at last, able to realise my long-cherished dream of an additional production hall.”
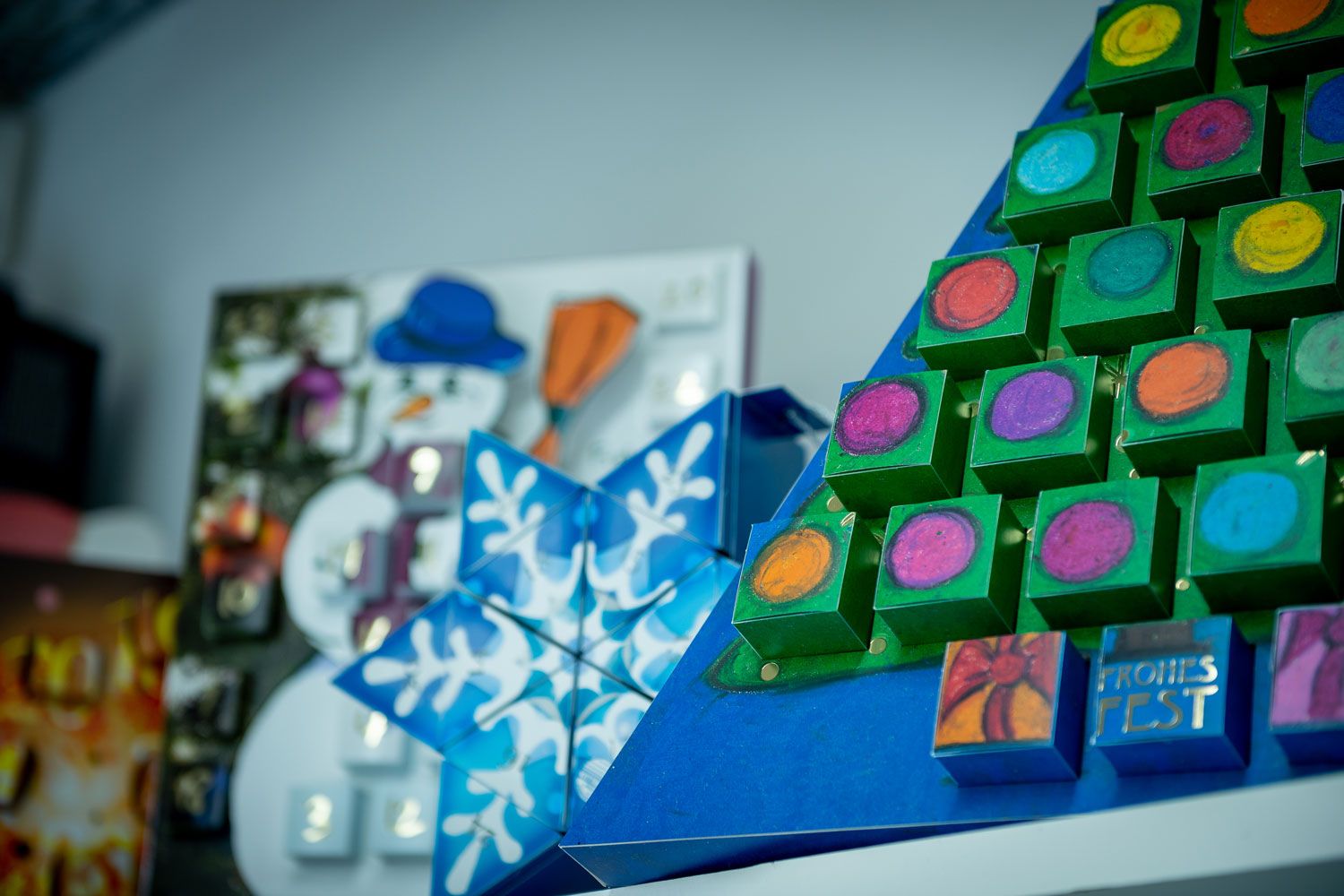