Valued customers report extremely high print quality and achieve top productivity
- Growing installation base recognizes outstanding value at budget-friendly entry point
- Guiding philosophy is to provide the highest level of unique service and support
- Broad product portfolio includes innovative and impactful technologies
In response to the ever-increasing demand for flexible packaging, Koenig & Bauer is taking a leadership position as it positively responds to its growing customer base with a broad product portfolio, outstanding value, and strong service and support.
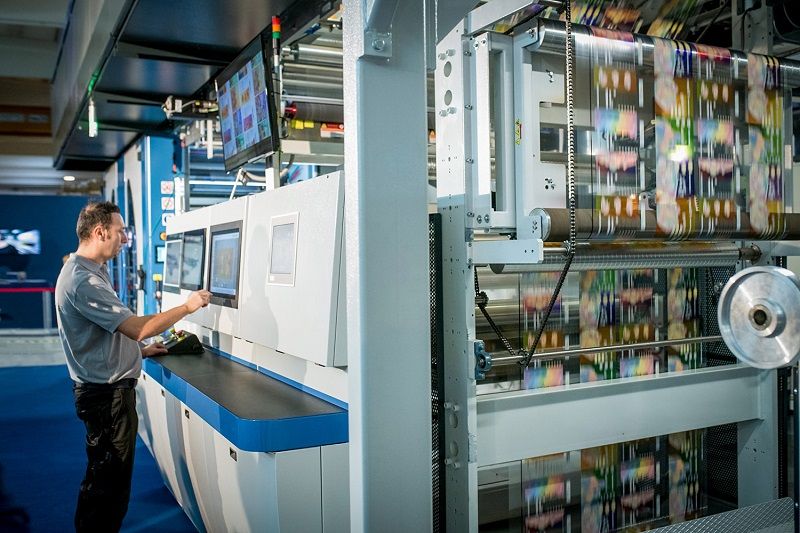
Koenig & Bauer XG press in action producing high quality flexible packaging
AR- DataGlass
In today’s competitive market, many flexible packaging printers are finding that orders are smaller with shorter lead times. Being able to remain fully operational to produce these orders is a necessity. Real time service support is one of the premium methods offered by Koenig & Bauer. It has developed its own remote maintenance and modern communication channels known as Augmented Reality-DataGlass Remote Support.
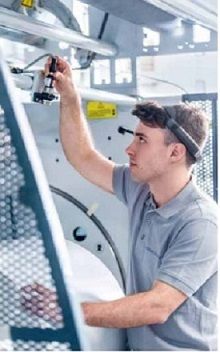
At a 2019 Flexographic Technical Association’s (FTA) InfoFlex meeting, Koenig & Bauer received the FTA’s Technical Innovation Award for its Augmented Reality-DataGlass Remote Support. This system provides Koenig & Bauer remote maintenance specialists with the ability to experience, in real time, what a customer’s technical team can see and hear.
“Koenig & Bauer and its AR-DataGlass technology has enabled us to increase our uptime and supports our goal of providing consistent, high quality printing that our customers have come to rely on,” says Beth Smith, director of marketing at Great American Packaging, a Los Angeles-based supplier of flexible packaging. “We continue to grow our applications and further enhance our press’ total capabilities.”
Evo XG
Flexo printers who are seeking the highest quality and productivity are turning to Koenig & Bauer Evo XG highly automated flexo press for processing film sheets, paper and cardboard at production speeds of up to 600 m/min.
In all versions of the Evo XG, solvent as well as water-based inks can be used, as well as curing inks (UV / EB). The configuration of the Evo XG with additional individual printing units using flexo or gravure printing technology is a further option for extending the performance range of the press. True-to-register printing, varnishing, coating or laminating in recto and / or verso printing are thus possible.
“The Evo XG is precisely the kind of machine we were looking for. We are convinced that we have made the right decision and that we will now be able to further strengthen our position as European market leaders,” said Jürgen Popp, owner and managing director of Zöllner-Wiethoff.
“The print quality of the Evo XG is outstanding and gives us new capabilities that enhance our customer portfolio and product positioning,” says Louis Figueria, director of printing at Yellowstone Plastics, a supplier of flexible packaging located in Idaho Falls, ID. “The press shows the true capabilities of high quality flexo printing.”
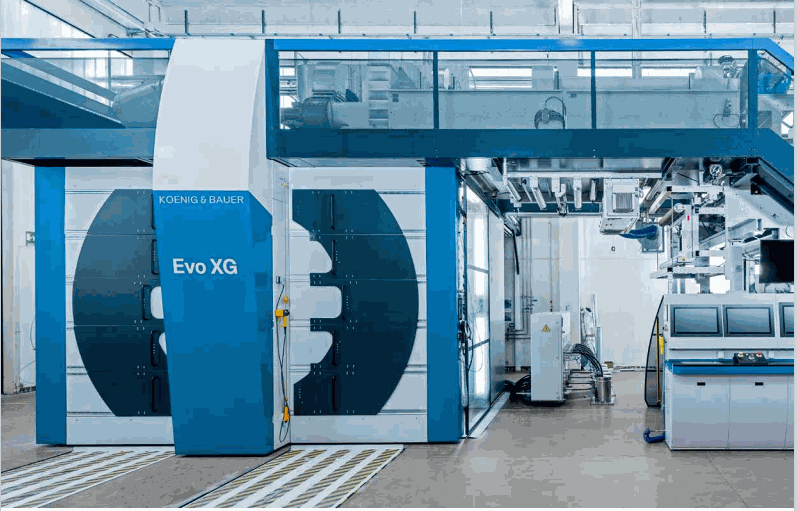