Powder is used to prevent backlash and for better drying of printed works through oxidation and creates a gap between the printed sheets.
Powder does not cause drying. At the same time, powder can improve the sliding behavior of printed sheets in the machine and in the finishing steps after printing.
Various printing devices and systems have a powder spraying system. Their common goal is to spread a small amount of powder evenly throughout the sheet.
Classification of drying powder
Powder is made of different materials and in different sizes from 10 to 80 microns.
The most important factor of powder quality is the homogeneous sorting of powder size.
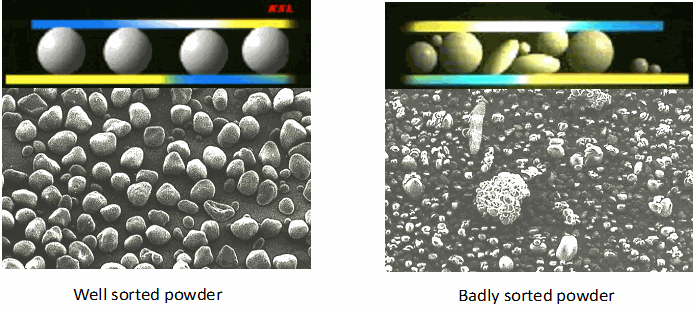
There are three main types of powder:
•Powder made of calcium carbonate (a product of inorganic and mineral materials)
• Powder made from natural starch (vegetable product)
•Powder with sugar base
powder with calcium carbonate base
Calcium carbonate drying powder is heavier, creates little dust (much less than starch and powdered sugar) and can be used in smaller quantities.
The crystal structure of calcium carbonate can lead to the roughness and sanding of the printed work and it damages the plate and parts of the machine.
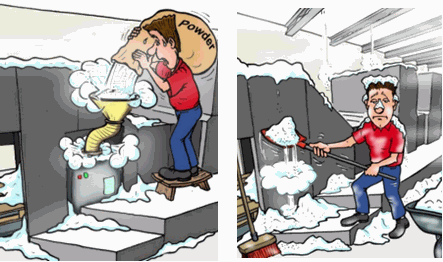
Common problems associated with drying powder
Uneven powder distribution.
Powder nozzles or path tubes are blocked or disabled.
The air of the blowers (wind on the job) is very strong in delivery.
The air suction is very strong.
Testing the performance of powder spray nozzles
Check the application of the powder in the machine with a black sheet (printed paper or by printing zinc).
You can also use an old blanket.