- Eight-colour press for 4-over-4 perfecting with additional inline coating
- Inline quality control even includes grey balance measurements
- Elegant print products for customers with particular expectations of quality
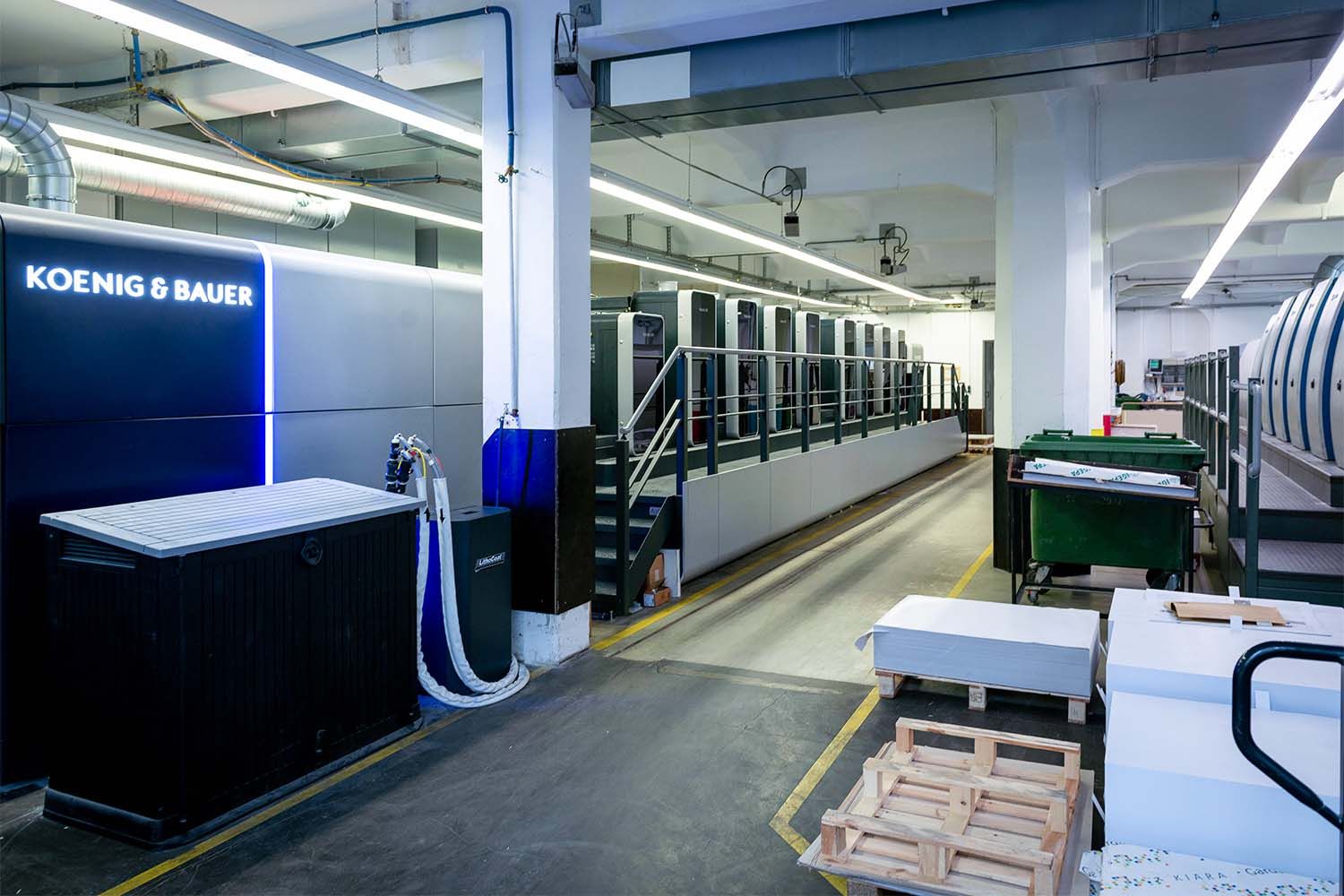
Rapida 106 double header: on the right is a five-colour coater press dating from 2010, and on the left the new eight-colour Rapida 106 X with perfecting unit and coater that went into production in August 2021.
And a reputation like these spreads quickly. Art museums, architectural design studios, photographers, publishers and agencies all entrust their work to DZA, especially when it comes to printing catalogues
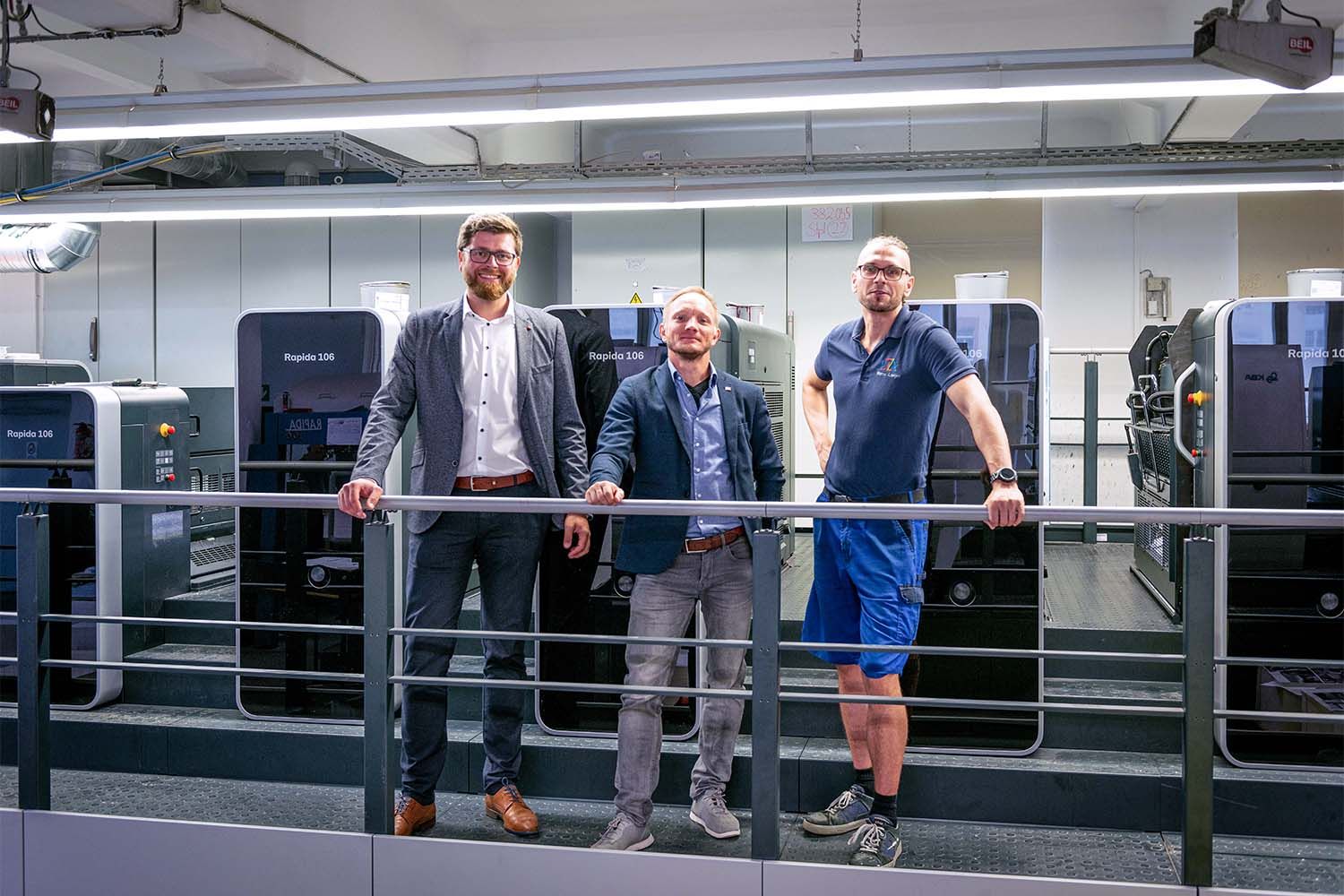
Left to right: Oliver Fuchs, Koenig & Bauer Germany, Peer-Philipp Keller, DZA managing director, and Olaf Feistel, DZA print department manager, at the highly automated Rapida 106 X.
Quality control all the way down to the last detail
At DZA,They always have used very latest press technology in action. For a few weeks now, the company has been printing on a brand new Rapida 106 X. With eight printing units, a perfecting unit for 4-over-4 production and an additional inline coater, the medium-format press (max. sheet format 740 × 1,060 mm) is the company’s most developed sheetfed offset installation to date.
And one which uses quality measurement and control systems. QualiTronic ColorControl ensures consistent print quality. The system also utilises InstrumentFlight for grey balance control and QualiTronic PDFCheck for a comparison of each printed product with the pre-press PDF.
Even special sensors detect coloured and black substrates both at the infeed and when the sheets are turned in the middle of the press.
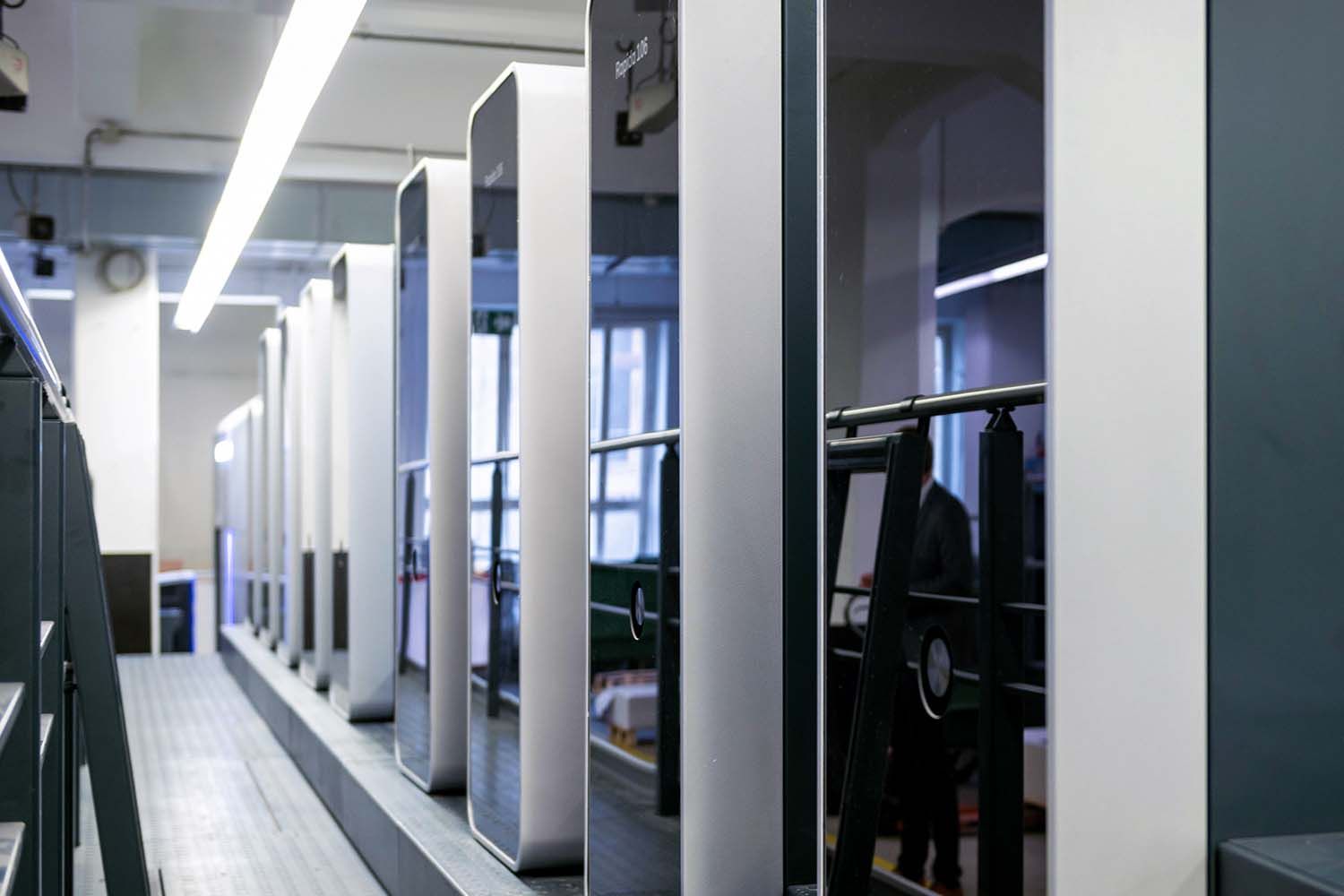
Automation for fast job changeovers
With the concentration on mainly short to medium run lengths, the DZA specialists placed particular importance on makeready-saving automation solutions when configuring the new press. This begins with simultaneous plate changing (DriveTronic SPC) and applies equally to the washing systems (CleanTronic Synchro). Parallel processes are standard here. After all, “when there are ultra-short runs of just 250 to 500 copies, the printers have their work cut out to keep pace,” says managing director Peer-Philipp Keller. It is for this same reason that the Rapida106 X seldom runs at full speed.
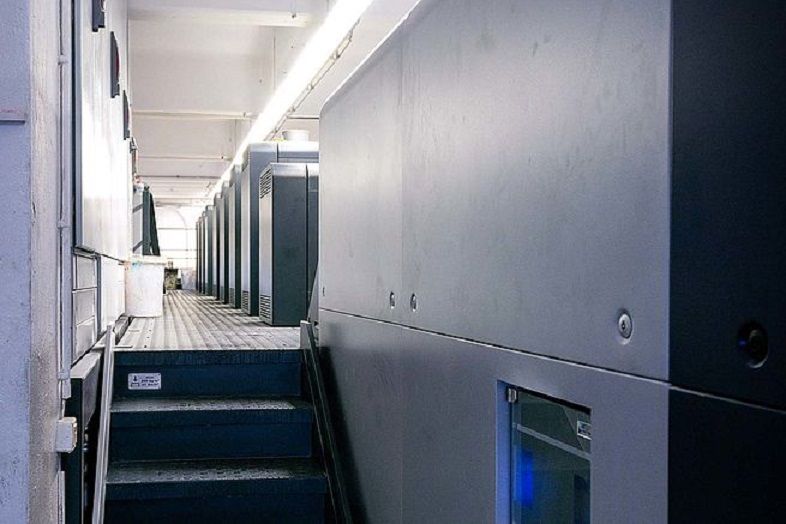
Numerous modifications – for example to the gallery design – were necessary to fit the new press into the existing production hall.
“Every product is unique”
Many jobs are printed with FM screening. Optimisations in pre-press and the use of highly pigmented inks enable printing with an extended colour gamut. And spot colours are also used where necessary to achieve specific colour tones and effects.
Versatility is one of the most important hallmarks of the print company. “Every product is unique!” – as is the firm conviction of Peer-Philipp Keller and his 75 employees. And that is also how every print job is treated. Experimenting and testing to realise the creative new ideas that product designers have come up with are daily routine for the production department in Altenburg. This applies not only to their printing services, but also to product finishing and bookbinding.
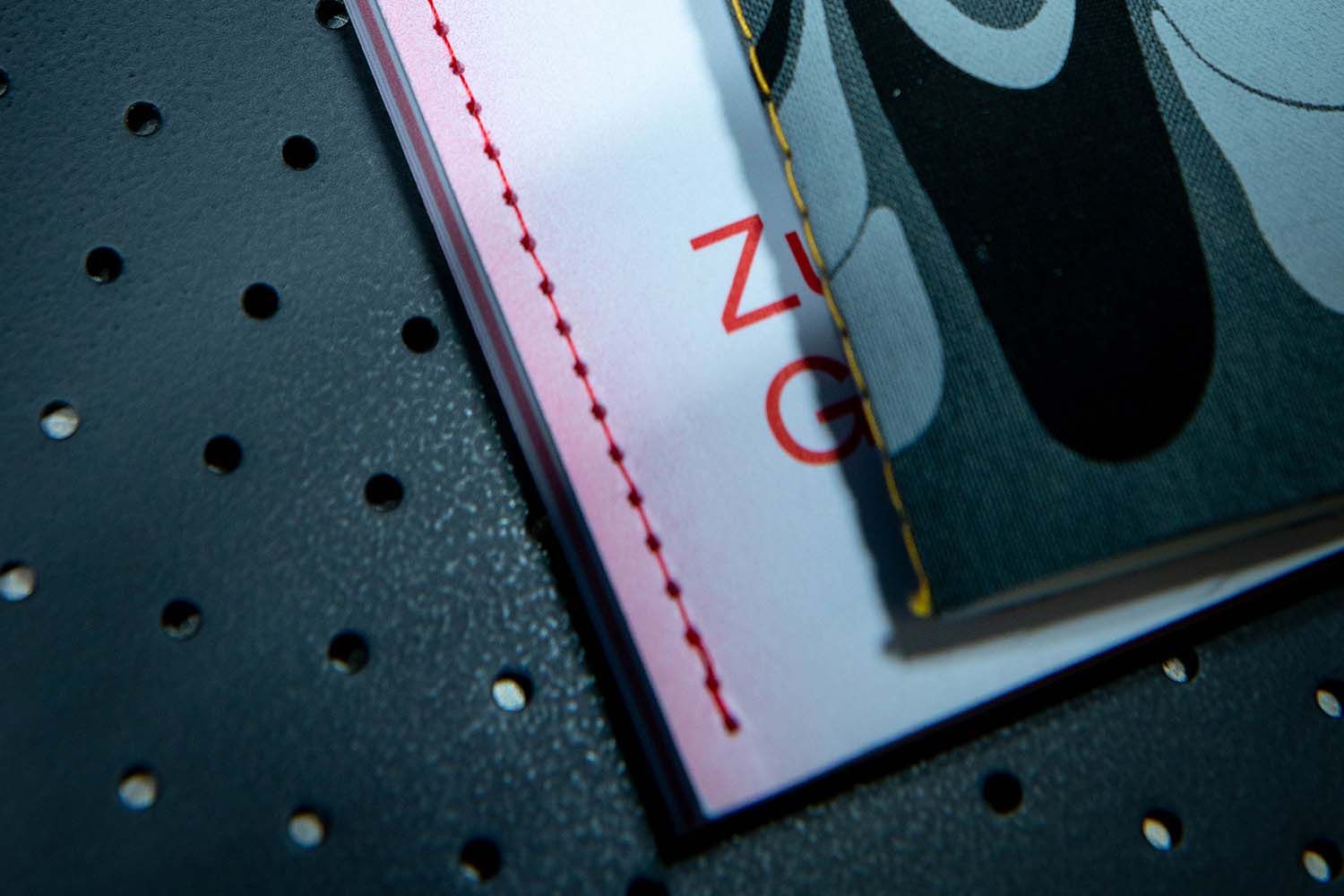
Lock-stitch bindings are one of the less frequently requested techniques. DZA can, of course, oblige.
A string of prizes – most recently at the Druck & Medien Awards 2021 – bears witness to the extraordinary print products made by DZA. A book about artist Meret Oppenheim, for example, received a coveted ‘Golden Letter’, the highest award presented annually by the Stiftung Buchkunst. And this award, in turn, closes the circle back to the proverbial silver type that is said to have been used in the company’s workshops in the past.