Printing engineers are frequently involved in heated debate regarding the factors that influence the results achieved by a particular printing method, especially in offset printing. This debate largely centres on the press and the relevant printing process because this is where all the components needed for printing come together. However, the print result also always reflects the interplay between the materials and resources used and the operating personnel. This series of articles will explain the various factors separately and describe them in detail.
The diagram below shows the most important factors. The pressroom climate is an additional factor, but this will not be considered due to the significant regional differences.
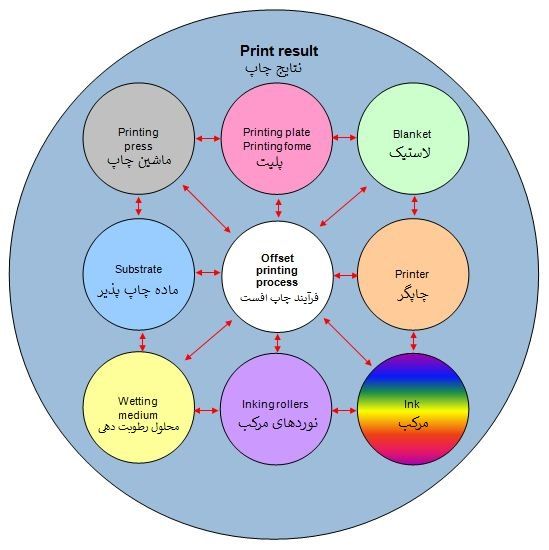
Each of these factors has a significant impact on the print result and is directly linked to the other parameters. While the last edition of Gallus In Touch took a closer look at printing plate parameters, this issue will focus on blanket parameters.
Rubber blankets
The diagram below shows the most important blanket parameters that influence print quality and the print result.
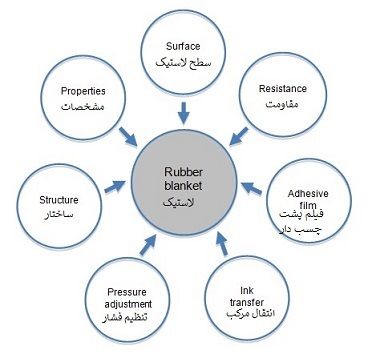
Blanket structure:
The structure of a rubber blanket, which must also be able to absorb tangential thrust forces (flexing), has a key impact on its tear strength, stretchability, compressibility and resilience. That's why compressible blankets are normally used.
Sample structure of a UV blanket:
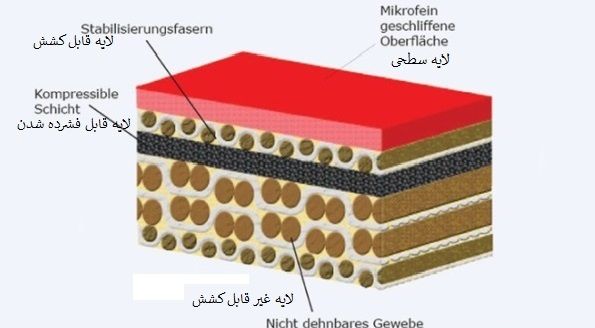
The weft and warp direction are also important. The warp, which is indicated by lines on the back of the blanket, always runs in the direction of printing
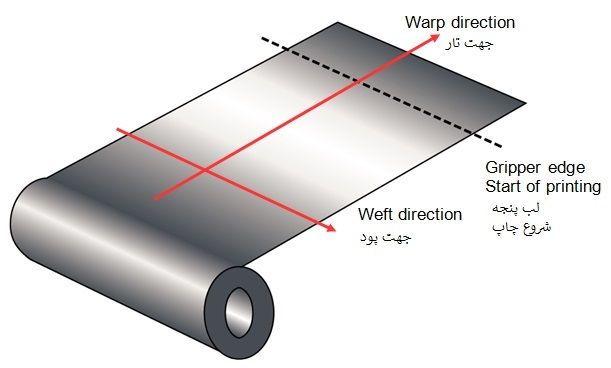
Ink transfer and printing pressure adjustment
Ink transfer from the printing plate via the blanket to the substrate is a key factor in ensuring good print quality. The blanket's surface texture is particularly important in this respect.
Adequate pressure adjustment between printing plate cylinder and blanket cylinder and between blanket cylinder and impression cylinder (substrate) is essential for good ink transfer. In halftone printing, the deformation/enlargement of screen dots must be minimised. This dot gain can vary depending on the blanket used, as the following printing characteristics show.
Printing situation between printing plate and blanket
The diagrams below show the flexing behaviour in the printing zone between plate cylinder and blanket cylinder. With a compressible blanket, pressure adjustment compresses the compressible layer. With conventional blankets, the rubber layer is compressed on the surface, which creates a rolling bulge. A similar thing happens in the printing zone between blanket cylinder and impression cylinder. When using compressible rubber blankets, the screen dots in the printing zone are subject to the least deformation and also adapt better to the substrate surface. They are therefore not affected by different thicknesses in the substrate web, e.g. glueing points that could compress the blanket.
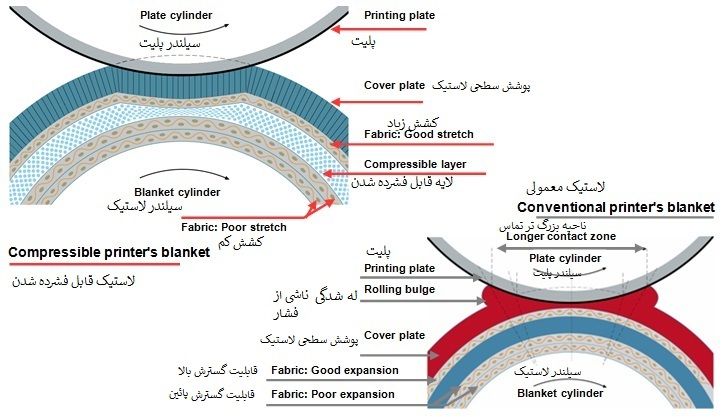